CONDITIONING METHODS EVALUATION
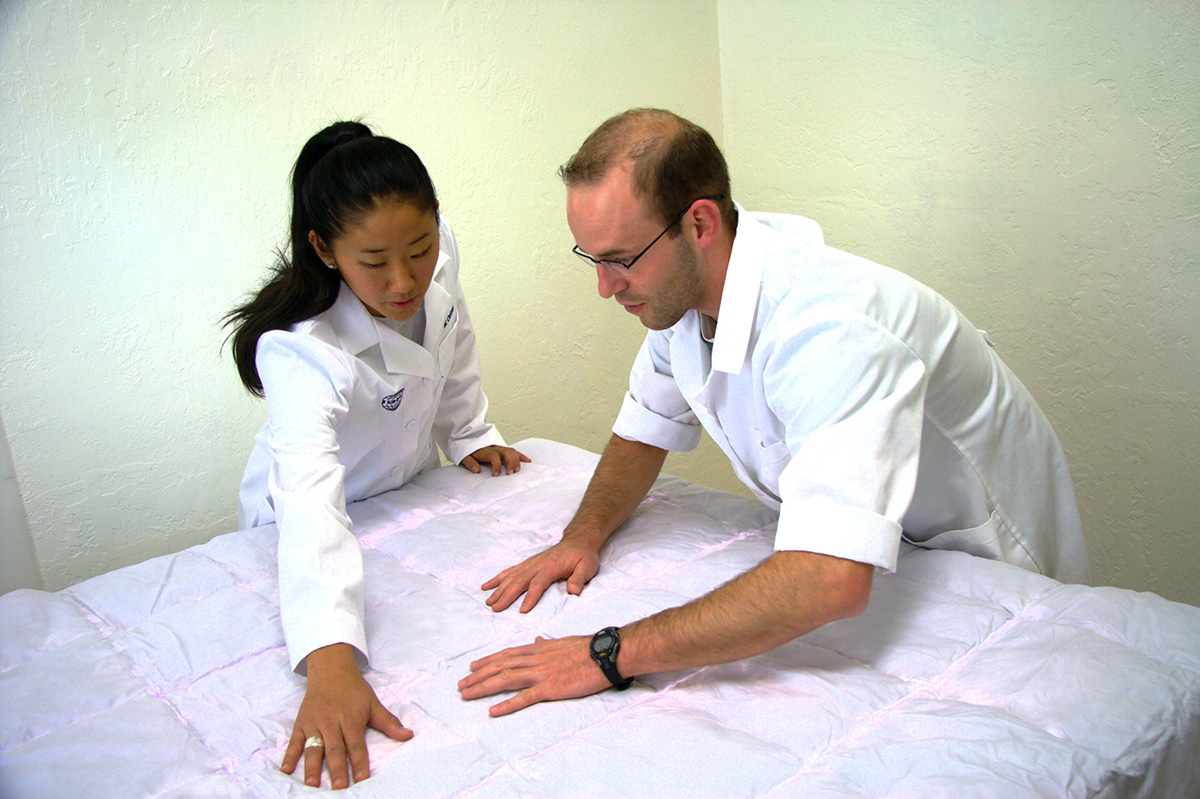
Fill Power testing has undergone dramatic changes throughout its continuing evolution. These changes have all helped to improve the reliability and reproducibility of Fill Power testing.
Two main questions are always asked by buyers of both bulk down and feathers as well as finished products:
- What is the original Fill Power of the bulk down and feather filling material that we purchased?
- What is the “usable” Fill Power of the down and feathers that the end consumer will experience while using the product?
Many different measuring systems and cylinders exist to measure Fill Power:
- IDFB - Lorch mm/30g
- IDFB - Lorch cubic inches/ounce
- EN 12130 - mm/20g or cubic cm/g
- Old USA Cylinder - cubic inches/ounce
- JIS Cylinder - cm/30g
- New JIS Cylinder - cm3/g
- China GB/T Cylinder - cm/28.5g
- China FZ/T Cylinder - cm/28.5
All of the above systems can be converted to the approximate value of another system with standard factor tables. The conversion does NOT take into account the conditioning method. The only accurate Fill Power result for the different methods is to test according to the specific method.
The most critical part of Fill Power testing is the conditioning method. Any of the conditioning methods can be used with any of the cylinders and measuring systems. Most countries and regions specify which conditioning method should be used with which cylinder.
The following pages describe the conditioning methods and the chemical/physical reasons why conditioning is important for testing Fill Power.
Brief Explanation of the Seven Different Conditioning Methods
1. No Conditioning
Down processors often use no conditioning to measure Fill Power immediately after washing and sorting down & feathers.
2. Oven Heating GB/T
The Chinese GB/T conditioning method for Fill Power requires down to be heated at 70 C for 45 minutes and then conditioned in a textile climate room for 24 hours before testing.
3. Oven Heating FZ/T
The Chinese FZ/T conditioning method for Fill Power requires down to be heated at 50 C for 60 minutes and then conditioned in a textile climate room for 24 hours before testing.
4. Box Conditioning
Down and feathers are placed in a conditioning box for 72 hours in a textile conditioned room (20C ±2C and 65% RH ±4%)
This conditioning method has been used for decades. Most test methods including EN 12130 and IDFB have required this conditioning method for many years.
5. Tumble Dry
IDFL developed the Tumble Dry conditioning method in 1996. IDFL published initial results of our research in January 1997.
In 1999, the IDFB officially adopted the Tumble Dry conditioning method as part of its Fill Power method. Europe also adopted the Tumble Dry method in the PAS 1003 document in 1999. IDFB has since cancelled this method as an official method.
6. Water Rinse
IDFL developed the Water Rinse conditioning method in 1996 and published results of our research in 1997. The water rinse method is a good indicator of Fill Power after a consumer washes a down product.
7. Steam
Japan developed a Steam Conditioning method in 2004. IDFL and the Japanese Down and Feather Association developed a revised steam method 2005. The IDFB Technical Committee voted to adopt the Steam Conditioning method during the Kyoto IDFB meetings in June 2005. Steam is the only active IDFB approved test method.
The Interaction of Down and Feathers with Moisture and Temperature
Down and Feathers (chemically very closely related to human hair) consist of natural macro-molecules. These are based on proteins, which in turn, are assembled of various amino acids. The entire family of these organic chemicals work in a physical-chemical interaction with water molecules. As for down and feathers, the moisture content reaches an equilibrium of approximately 11 % at close to standard climate conditions (23 C and 60 % relative humidity).
The natural construction (3-dimensional arrangement of molecules) of each individual down or feather has a very stable form. Unless chemically or thermally mistreated, no matter how hard the down is twisted or compressed, it can (like naturally curly hair) return to its original form. In metallurgy this phenomenon isknown as “memory effect”. In the case of the protein macromolecules (the building blocks of down andfeathers), warmth and moisture support this (re-)activation of the structural memory.
When customers use a duvet, a sleeping bag or a down jacket, they exude moisture and warmth and thedown cluster “opens up”. This helps to increase the insulation value of the product, which may have beenhard compressed for a long period of time. Customers may become more happy with the new duvet after use. The effect may continue after the first use and improvement may occur after 2 or 3 nights.
For this reason, in quality testing, the final readings of Fill Power are usually measured after 3 to 4 days. For the same reason, and to simulate this positive human influence on the Fill Power or loft of a down product, various conditioning method were developed.
Development of Conditioning Methods to Mimic use of Down by consumers
The Tumble Dry conditioning method, developed by IDFL in 1996, was a big step in the development of a method to accurately measure the insulation capability of down and feather products. In 1996, IDFL also proposed the Water Rinse method. The Water Rinse method was developed specifically because some products (especially compressed jackets and sleeping bags) did not respond properly to Tumble Dry.
The tempo of a chemical reaction is accelerated by a factor of 2 with each 10C rise in temperature. Down and feathers are washed and dried at high temperatures. Original Fill Power is determined by the Fill Power test that occurs immediately after washing and sorting at the down factory.
The industry has always searched for a method that could reproduce the original Fill Power tested at the down factory. Tumble Dry was a great improvement over the Box Conditioning method. However, Tumble Dry was not entirely successful at reproducing Fill Power for products that had been compressed for several weeks during shipment.
Japanese manufacturers worked to find a method for reproducing the original Fill Power that was tested at the down and feather washing factory. This goal was achieved by applying a concentrated form of moisture (steam) and higher temperature (hot steam).
IDFL began a series of several thousand tests comparing original Fill Power with Fill Power after various shipping and compression techniques. IDFL baked down for several hours, compressed down with 1000 pounds of pressure, repeatedly washed down products, and vacuum packed products for several weeks. After all the thousands of tests IDFL came to the conclusion that the Japanese steam method was the only method that successfully reproduced the original Fill Power value regardless of the harsh handling, shipping and compression of finished products.
Which Fill Power Conditioning Method is the most Accurate?
This is a good question and can be answered in two parts.
Original Fill Power
Original Fill Power is defined as the Fill Power tested immediately after washing and sorting at the down factory. The steam conditioning method is the only method that will accurately reproduce the original Fill Power of down and feathers regardless of the shipping, compression or other handling.
Usable Fill Power
The usable Fill Power is a very difficult value to determine. Many factors influence the usable Fill Power. Some factors outside of the filling include:
- Filling Density of the finished product
- Product construction
- Fabric type
- Use of additional fabric covers for duvets and pillows.
The following chart outlines the reliability of three conditioning methods for determining original Fill Power and “usable” Fill Power.
Conditioning Method | Evaluation of Accuracy for Testing Original Fill Power | Evaluation of Accuracy for testing Usable Fill Power |
---|---|---|
No Conditioning | Down Processing Factory normally uses no conditioning when measuring Fill Power after washing and sorting. “No conditioning” will never give accurate original Fill Power values after shipping. | “No conditioning” will give an accurate Fill Power for the “as is” condition of a product. However, this Fill Power value does NOT reflect the increase in Fill Power that occurs after a consumer uses a jacket, sleeping bag or comforter. |
Oven Heating GB/T | This method will not give accurate original Fill Power values. | This method gives similar results as Box Conditioning. In some cases results are lower. |
Oven Heating FZ/T | Similar to GB/T method. | Similar to GB/T method. |
Box Conditioning Method | This method will not give accurate original Fill Power especially if the product has been compressed. | Box conditioning will NOT give an accurate “usable” Fill Power value. The method does not take into consideration the change in Fill Power after a customer sleeps under the duvet or in the sleeping bag. |
The following chart compares the reliability of Tumble Dry, Water Rinse and Steam Conditioning to determine both original Fill Power and “usable” Fill Power.
Conditioning Method | Evaluation of Accuracy for Testing Original Fill Power | Evaluation of Accuracy for testing Usable Fill Power |
---|---|---|
Tumble Dry | Tumble Dry Fill Power tests will give a result much closer to original Fill Power than Box Conditioning. | Tumble dry is not a good indicator of “usable” Fill Power. Several reasons are listed below: |
Water Rinse | The Water Rinse method gives a Fill Power value that closely matches the original Fill Power. | The Water Rinse method gives a possible “usable” Fill Power value on a finished product by mimicking the washing and cleaning by the customer. |
Steam | The Steam Conditioning method is the most accurate method to determine the original Fill Power value. | Steam conditioning gives a more consistent result regardless of product handling before sending to the test lab. |
Additional Information for Rating Tumble Dry and Steam Conditioning Methods
Steam Conditioning is the only accurate method to determine the original Fill Power. This test should be done to verify the Fill Power of bulk down purchased from the factory.
Evaluating “usable” Fill Power is more complicated. The following information should be considered when evaluating the conditioning methods:
- Both the Tumble Dry and Steam methods add moisture and heat to the down and feathers.
- Several thousand test results have since proven that Steam conditioning does NOT falsely inflate the Fill Power beyond its natural, original structural value.
- The steaming process “adds” moisture and heat to the down during steaming. The down is immediately revived with warm, dry air. This process simulates the factory washing process of bulk down and the consumer washing of finished down products.
- The Tumble Dry process also “adds” moisture and heat to the down during the tumbling with a damp cloth. The down is moderately “steamed” and revived as the cloth is dried.
- The steam method revives to a steady state as early as 24 hours after conditioning. (IDFL recommends that Steam Fill Power always be tested after 72 hours). The Tumble Dry method requires 72 hours to revive to a steady state.
- The Tumble Dry method can be manipulated by handling of products before shipping to the test lab.
- The Steam method gives similar results regardless of the handling of the product before arrival at the test laboratory.
Conclusions
Steam Conditioning is the only consistent, reproducible method of determining the original Fill Power. The official IDFB method is designed to determine original Fill Power.
“Usable” Fill Power is more complex and depends on the product construction and other external factors.
Tumble Dry is supported by some organizations as giving more accurate “usuable” Fill Power. However, Fill Power results using Tumble Dry can be manipulated by handling of the product before sending to the lab.
Even though IDFL developed the Tumble Dry method, IDFL supports the Japanese-developed Steam Method as the basis for determining accurate, consistent Fill Power.
The Steam Conditioning method gives the most consistent Fill Power result and is therefore the best method to determine both original and usable Fill Power.