DOWNPROOFNESS VS. AIR PERMEABILITY
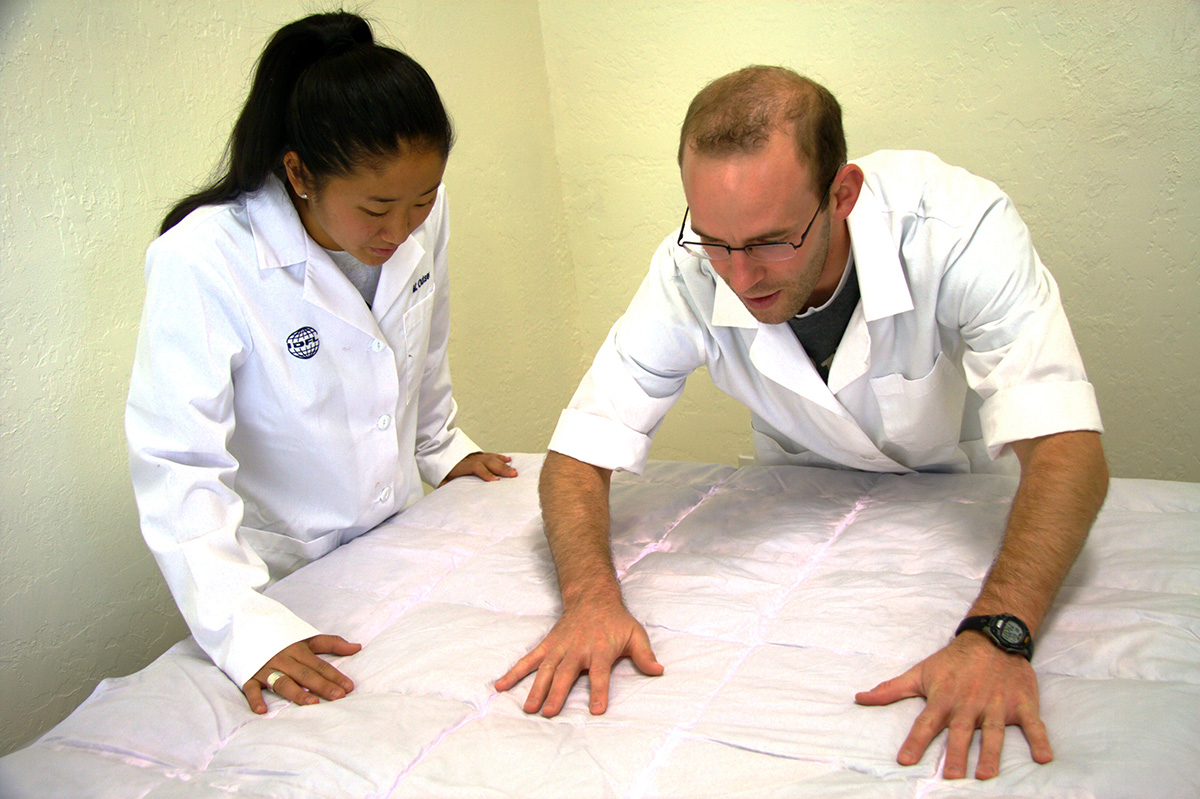
One of the most common misconceptions is that downproofness can be predicted using a fabric’s air permeability value. There is some logic to this reasoning; if more air passes through the fabric, it would make sense that more plumage would also get through. While there are a few cases when this is true it cannot be assumed in all cases.
What is the Air Permeability number?
Air Permeability is the number of cubic feet of air passing through a square foot of fabric per minute (or liters per square meter per second), expressed as: ft3/ft2/min (or liters/m2/sec). Apparatus: Frazier® High Pressure Air Permeability Instrument.
What does the Air Permeability number mean?
Generally, for cotton fabrics numbers below 8.0, and for synthetics numbers below 3.0 are desired for downproofness. Lower air permeability numbers indicate the reduced ability for air to pass through a fabric. However, a low number also indicates that a fabric will be less breathable.
For cotton an 8.0 or for synthetics a 3.0 or below indicates a greater likelihood that the fabric is downproof. However, certain fabrics may have a good air perm number (< 8.0 or < 3.0), but fail the downproof test. And, other fabrics may have poor air perm number, but pass the downproof test.
What is Downproofness?
Downproofness is a fabric’s ability to contain down and feathers. The test involves placing a test pillow into a rotating box where it is tumbled for 30 minutes, during which time it is struck by rubber stoppers. This procedure attempts to mimic the actual use of the product. Downproofness is considered poor when many fibers and/or feathers are able to pass through the fabric.
How does the Downproofness rating system work?
The rating (only used in the Rotating Box method) is based on a scale from 1 – 5 (with 1 being the worst and 5 being the best). The rating is derived from the number of fibers and/or feathers that pass through the fabric of a test pillow
How is Air Permeability related to Downproofness?
As each test measures a different physical aspect of the fabric, the numbers are often unrelated. One measures the transmission of air through a fabric, while the other measures the physical transmission of down/feather material through a fabric. This is why IDFL recommends both tests be performed on a fabric sample. Each test has separate benefits and can be interpreted differently.
Downproofness Versus Air Permeability Comparison
As seen in the chart below, there is a large cluster of data points near downproof results < 10 fibers and air permeability values < 8 CFM. These values are considered the upper limit for a cotton fabric to be considered downproof. But there is also a large portion (approx. 21%) of samples that achieved “passing” air permeability values but failed downproof testing. And there are also a few samples that had very high air permeability values but still passed downproof testing.
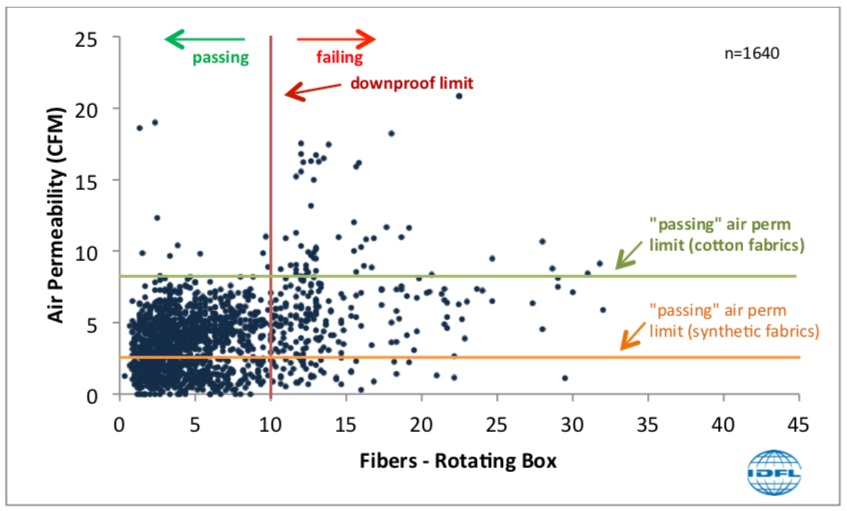
In addition, to evaluate the correlation between downproofness and air permeability, we use the **Pearson Correlation Coefficient (r).
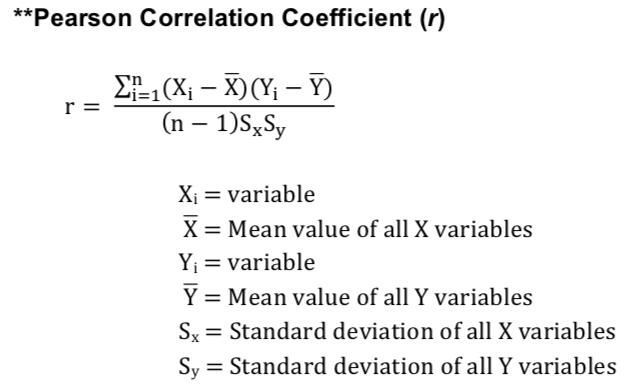
When there is a perfect correlation, the plot (Chart 1) of downproof grades vs. air permeability readings lies along a straight line and the Pearson Correlation Coefficient (r) will be equal to 1 or -1. Using data from past IDFL samples, the correlation coefficient (r) was equal to 0.451. This suggests some relationship, but not enough to make any significant inferences.
Recommendation
Based on the above data and information, it is clear that air permeability cannot always predict downproofness. To determine a fabric’s actual downproofness, it is best to do the physical downproof testing.
In addition to fabric downproof testing, it may be beneficial to test the downproof of finished products or prototype panels. Finished product downproof testing evaluates the migration of leakage or filling materials in an entire sample (jacket, vest, prototype, etc.). This test of the actual finished product can help improve performance by evaluating the source and/or location of leakage.