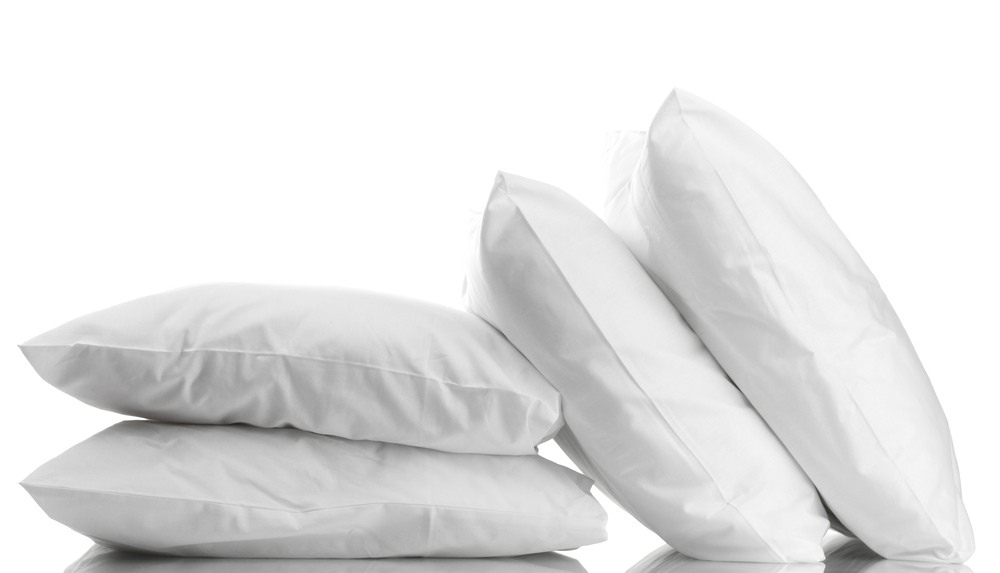
Down and feather products requires on-going, frequent testing because the raw material is a natural product and very non-homogeneous. Each shipment can vary in a number of factors.
Testing is time-consuming because the acceptable methods require tedious work by hand. Machines cannot perform the separation task for specie and content analysis.
Testing of Raw Down and Feather Material by Feather Processors
- Testing of every raw shipment of down from an exporter or farmers cooperative is usually required to ensure the material meets specifications. Each bale of raw product can contain different mixes of down and feathers. A small amount of material is taken from 10-20% of randomly selected bags, then mixed and sent to a laboratory (such as IDFL) for testing.
- After the material is washed and sorted, testing is again required. The sorting machines are adjusted continually. The washing and sorting process can change the down and fiber mix of material. Some feather processors will test every single lot of down that is processed. Others perform random spot checks to ensure material meets expected values.
Testing of Down and Feather Material by the Finished Product Manufacturers
- The incoming washed down and feathers should be evaluated.
- Several manufactures require a certification with each shipment.
- Several manufacturers test every shipment.
- Other manufacturers perform random tests on every type of material received.
(Some material will come in multiple shipments from a feather processor.)
- Testing should also be completed after the finished products are manufactured. This will verify that the correct fill material was used and that the manufacturing process did not adversely affect the fill material.
This finished product testing will also replicate tests the retailer or government enforcement agencies will perform.
Cost effective Quality Assurance programs for down and feather products are a challenge because the material is a natural product and very non-homogeneous.
Objectives of a Quality Assurance Program
- Make suppliers aware that testing will be ongoing. If suppliers know that testing is ongoing by the receipt of test reports with problems, etc., the supplier will likely meet or exceed product specifications.
- Verify that products meet retailer specifications.
- Verify that products meet government regulations.
- Ensure that products can meet advertising claims.
Retail Testing Programs
Retailers and distributors have developed a variety of testing programs. Some of the current testing programs include the following:
- One retailer has the warehouse staff at each of 3 distribution centers pull one sample from every shipment and send to IDFL.
- Some retailers pull 3-4 random samples from each product group.
- Another retailer does random testing. If a problem is found, 3 pieces of each size are pulled for more comprehensive testing.
- One manufacturer tests one sample of every type, style and size of finished products. Random samples are taken from warehouses and retail shelves.
- Some retailers require the manufacturer to complete extensive testing, and the test certificates are forwarded to the retailer.
- Several retailers require the manufacturer to send samples at the beginning of a production run to IDFL for testing. This is followed-up with random spot testing of products after shipment.
The Vendor Specification
Specifications should be very clear for the vendor. The testing method and allowed tolerances should be indicated.
Minimum values for each characteristic of the product should be outlined.
Because of the nature of the product and testing variances, the method for determining product compliance should be outlined:
Option 1:
Every piece must meet minimum levels. The average value then will be higher than the specification. For example, if all pieces in a shipment must have at least 90% goose specie, the average specie for 5 products tested will likely be 93% or higher because the range of specie results on multiple products within a lot will be 90-99% goose.
Option 2:
The average of test results for multiple pieces of a product must meet a minimum level. The buyer might state that the average result of 3 pieces tested must be a certain level.
Down Material Tolerances
If the buyer specifies a product to be labeled "down", the buyer should indicate what tolerance system is
used or the buyer should specify their own tolerance.
- USA/ADA guidelines. ("DOWN" labeling requires a minimum of 75% down cluster and blends require exact disclosure of the down cluster %)
- Canadian regulations require 75% down cluster for "DOWN" -- but allow a 25% tolerance on blended products.
- Buyer specific regulation. (A minimum of 78% cluster for example.)
- The European Union has adopted revised requirements for EU countries.
Other government mandated specifications
- Oxygen Number (USA requires less than 20). Many companies have a stricter requirement such
as 10 or 8. Canada and some USA states are considering a new regulation of 10 or less. - Specie. The FTC requires a minimum of 90% goose before an item can be labeled goose. The EU requires a minimum of 90% goose on "pure goose" and 70% minimum on "goose".
Other Claims About the Finished Product
- Fill Power. If fill power is advertised, this claim should be verified. Fill power ratings are based upon tests completed after the down and feathers have been washed and sorted but beforeinsertion into garments or bedding products.
Often finished product fill power results are lower than the original fill power values. The "Steam" fill power test can be requested. This test can replicate the original fill power value before the finished product was assembled.
In some cases, rinsing jackets and sleeping bags will replicate the original fill power. Fill power results should be 5% of claimed fill power. - Dust/Turbidity. If "dust-free" or similar claims are made, the turbidity of the filling material should be checked. Some companies have minimum turbidities ranging from 200 to 550. The 550 minimum is common in Japan.
The higher the turbidity, the cleaner the fill material. - "White" Down/Feathers. No more than 3% dark feathers or down is allowed.
- Hypo-allergenic or super-clean claims. Manufacturers should have data to support the statement that their products are within the parameters they have set for hypoallergenic or super clean. Such material will have very low oxygen (usually around 3.2) and a very high turbidity (usually 450-500 or higher).
Fabric Testing
Fabric shells used in down products need to be downproof. To verify claims made of threadcount and downproofness, the following can be tested:
- Physical Downproof Test. This test involves tumbling fabric with down/feathers in a container with rubber stoppers. The amount of leakage is counted and downproofness is reported on a scale of 1-5.
- Air Permeability Test. This test measures airflow through fabric. It is a good indicator of downproofness. The lower the number the less likely it is to leak. However some fabric fails the air permeability test but passes the physical downproof test and vice versa. Normally an air permeability of less than 10 is considered downproof.
- Threadcount Test. Threadcount claims are common on down products. Normally, the higher the threadcount the better the downproofness. However the yarn size and weaving techniques make some high threadcount material unacceptable for down products and some low threadcount work just fine.
How Often Should Tests be Performed?
- Sample products from a supplier should be carefully tested before shipment. Suppliers should immediately be notified of variances from specifications.
- 2-3 pieces from each lot should be tested for new suppliers. This makes new suppliers aware that the buyer is doing extensive testing.
- For existing long-time suppliers, random testing of products should occur. To budget and schedule such testing -- a fixed dollar amount or a % of the total shipment value should be allocated to quality control testing. This allows the decision to test to be made at the beginning of the product year, rather than incremental decisions throughout the year.
- If multiple shipments of the same product are scheduled, the random testing should occur throughout the shipping cycle. Often, the initial shipment is good, but subsequent shipments have problems.
Ideas for Reducing Testing Charges
Many companies recover their testing charges in one of several ways:
- Elimination of costly returns and customer complaints.
- Invoking of penalties in contracts where specifications are not met.
- Requiring the vendors to absorb the testing in their bids for products.
A possible method for finding problems early in the production process is:
- Test extensively on samples for each product type. Share these results with suppliers if problems arise.
January Sample 1st piece: Content, Species, Fill Power, Oxygen, Turbidity, Net fill weight,Threadcount, Downproof, Dust Evaluation
February Sample 2nd piece: Specie, Fill Power (results on these tests were poor on 1st piece) - Test completely a few pieces from first production shipment
August Production Shipment: Perform all tests - For subsequent shipments perform random testing -- perform fewer tests concentrating on problem items.
September Production Shipment: Net Fill Weight, Fill Power. Threadcount
October Production Shipment: Content, Specie, Fill Power